Test von Bordnetz-Architekturen
Kunde: Ford Research and Innovation Center Aachen
Bereich: Automobilindustrie / F&E
Anforderung: Test von Bordnetz-Architekturen mit Spannungen bis zu 60 VDC
Umsetzung: Software: LabVIEW
Bordnetz-Architekturen prüfen
In Zusammenarbeit mit dem Ford Research and Innovation Center Aachen wurde die erste Ausbaustufe eines Prüfstandes realisiert, mit dem Bordnetz-Architekturen mit Spannungen bis zu 60 VDC getestet werden können.
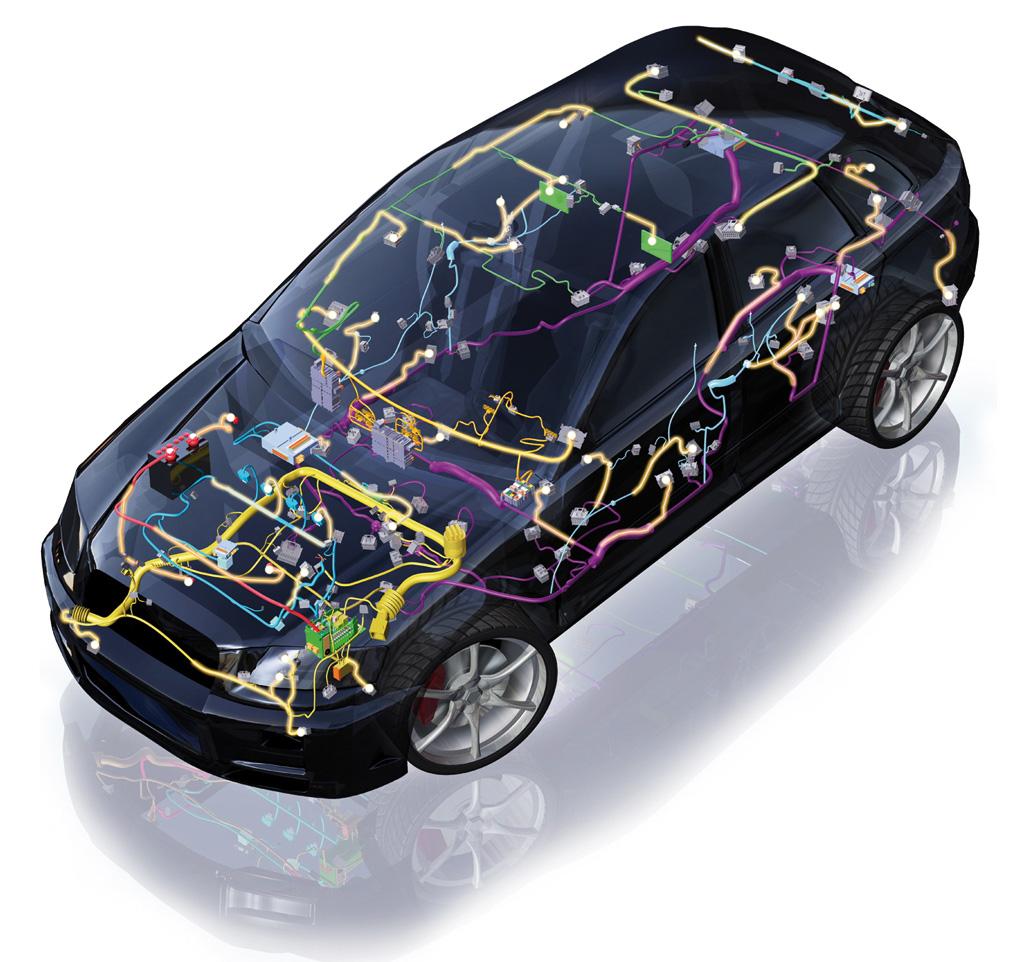
Bis vor einiger Zeit bestand das Bordnetz von Kraftfahrzeugen meist aus einer Lichtmaschine und einer einzelnen 12 Volt Blei-Säure-Batterie, die „einfach“ an ein Leitungsnetz mit ein paar wenigen Stromverbrauchern angeklemmt war. Die Einführung von Start-Stopp-Systemen und anderen verbrauchssenkenden Maßnahmen sowie viele zusätzliche Stromverbraucher, wie diverse Assistenzsysteme, erforderten neue Lösungen. Heute sind „intelligente“ Konzepte im Einsatz,bei denen die Komponenten des Bordnetzes über Bussysteme interagieren. Um die aktuell eingesetzten und die zukünftigen – auch für den Betrieb mit 48 Volt vorgesehenen – Komponenten einzeln und im Verbund testen zu können, entwickelt measX im Auftrag von Ford ein variables Prüfsystem.
Im ersten Schritt wurde die Grundlage für umfangreiche und variabel gestaltbare Tests an Akkumulatoren geschaffen. Dafür war es zwingend notwendig, das häufig bei modernen Energiespeichern vorhandene BMS (Batteriemanagementsystem) per CAN-Bus anzubinden. So kann die Batterie gegebenenfalls aufgeweckt und auf diverse Messdaten zugegriffen werden. Zudem wurde eine projektspezifische Signalkonditionierung mit verschiedenen Anschlüssen für elektrische Signale entwickelt: Zur Verfügung stehen jetzt – jeweils galvanisch getrennt – 16 analoge Eingänge und 4 analoge Ausgänge unterschiedlicher Spannungsbereiche sowie 14 Anschlüsse für Typ-K-Temperatursensoren, 8 optoisolierte 24V-Digitaleingänge und 8 frei belegbare Schließerkontakte.
Schnittstelle für Simulationsmodelle
Der jeweils zu untersuchende Prüfaufbau kann über eine Kombination aus programmierbaren elektronischen Netzteilen und Lasten mit bis zu 510A gespeist und mit maximal 1200A belastet werden. Ein geräumiger Klimaschrank erlaubt die Untersuchung der Prüflinge bei extremer Umgebungstemperatur und schützt durch seine integrierten Absaug- und Löschfunktionen den Prüfraum bei eventuellen Defekten an einem Akkumulator.
Um zusätzliche Umgebungsvariablen, Berechnungen und Steuerungsmöglichkeiten einbinden zu können, wurde eine Schnittstelle zu Simulationsmodellen implementiert. Beliebige Modelle, zum Beispiel aus MATLAB/Simulink, können angebunden werden.
Die Prüfungen lassen sich sowohl manuell als auch über automatisch ablaufende Testskripte steuern, die vom Bediener aus vorgefertigten Einzelschritten zusammengesetzt, parametriert und modifiziert werden können. Dabei können auch die variabel über CAN oder Simulationsmodelle verfügbaren IOs eingebunden werden.
Mit der Bediensoftware des Prüfstandes werden Testskripte erstellt, das Gesamtsystem konfiguriert, CAN-Datenbanken und Simulationsmodelle eingebunden, Messkanäle und -takte parametriert, das Mapping wichtiger Steuerungs- und Überwachungskanäle konfiguriert und Prüflingsparameter angegeben. Um die täglichen Arbeitsabläufe zu erleichtern, kann die Gesamtkonfiguration gespeichert, geladen oder in Teilen importiert werden.
Die eigentliche Ansteuerung der Prüfstandshardware, die Messwerterfassung, der Ablauf von Testskripten, die Ausführung des Simulationsmodells und die permanente Überwachung verschiedener Grenzwerte erfolgen auf einem PXI-Industrie-PC mit echtzeitfähigem Betriebssystem im deterministischen Takt von derzeit 1ms.
In der ersten Ausbaustufe des Batterietesters können Akkumulatoren getestet werden. Aktuell sollen Funktionen zum Test von Elektroantrieben und -generatoren sowie DC/DC-Wandlern ergänzt werden, so dass auch kombinierte Systemtests möglich sind.
Bild: © Delphi
Öffne X-Press mit dem Bericht als PDF